You might already be familiar with hydraulic linear actuators if you have seen a bulldozer lift gravel or sand off the ground. These machines work by converting hydraulic pressure to cause linear motion. Their simplicity and effectiveness make them ideal for a wide range of applications. Some examples are in aerospace, defense, heavy equipment, and manufacturing machinery.
This overview aims to cover the way hydraulic linear actuators work. You also discover their pros and cons, design considerations, and their applications. So, as a beginner or an expert in hydraulic systems, you are sure to learn a few things here.
Types of Hydraulic Linear Actuators
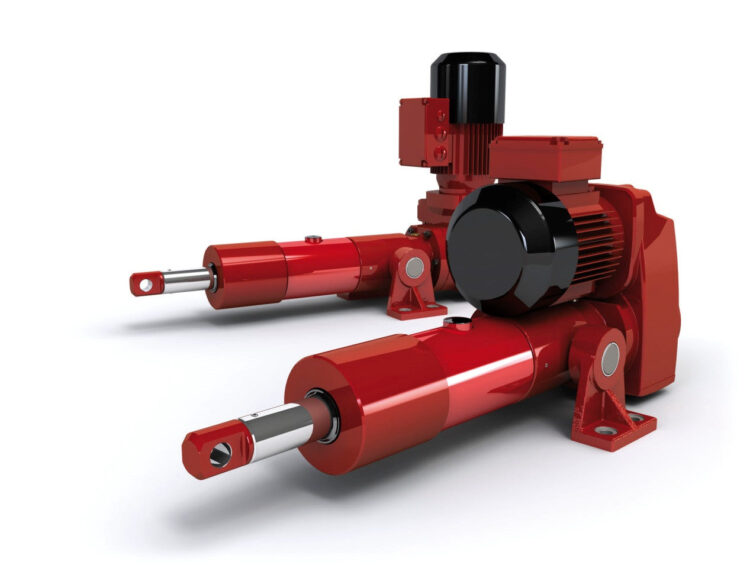
There are a few different types of hydraulic linear actuators. We have both the single-acting and double-acting models.
- Single-acting actuators rely on hydraulic pressure to extend the ram or piston. It uses a spring or similar mechanism to pull it back.
- Double-acting actuators, on the other hand, use hydraulic pressure to extend and retract the piston or ram.
Overall, hydraulic linear actuators are a simple and effective way to generate linear motion using hydraulic power. You can learn about other types of linear actuators here.
Components of the Hydraulic System
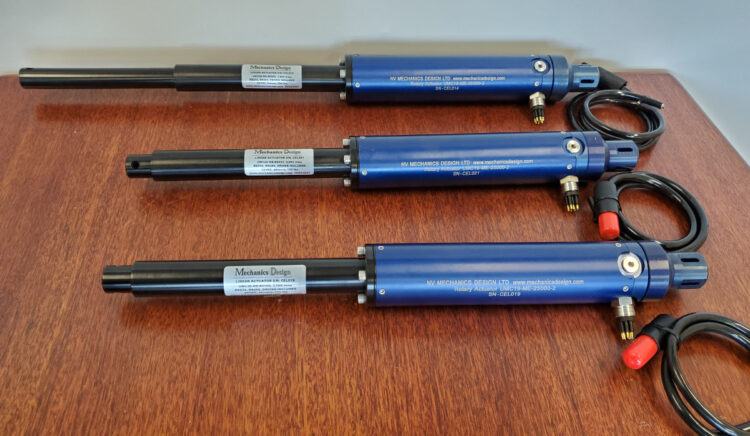
- Pump: The pump creates the hydraulic pressure for moving the cylinder. This happens when it draws the fluid from a reservoir and pumps it into the system.
- Cylinder: Meanwhile, the linear motion itself happens inside the cylinder. It consists of a piston that translates to and fro within the casing of the cylinder.
- Control valve: The control valve helps direct the flow of hydraulic fluid to the cylinder. By doing so, it controls the speed and direction of the actuator.
How Hydraulic Linear Actuators Work
Hydraulic linear actuators are devices that use hydraulic pressure to produce linear motion. The operating principle behind them is pretty simple. When acted upon, hydraulic fluid flows into a cylinder which pushes a piston or ram inside it. This, in turn, generates linear force. Here is the stepwise mechanism of how hydraulic linear actuators operate:
1. Conversion of Hydraulic Pressure into Linear Motion
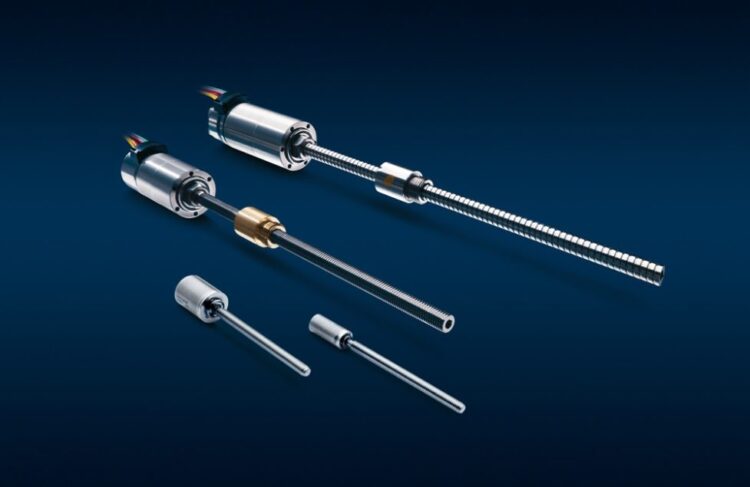
First, the hydraulic pressure causes the piston to move. It then moves the load attached to the actuator. In other words, the amount of force originating from the actuator depends on the pressure applied to the hydraulic fluid.
2. Role of the Piston and Cylinder
The piston and cylinder work together to convert hydraulic pressure into linear motion. The cylinder contains the piston inside, sealed using o-rings or seals to prevent fluid from leaking out.
3. Control of Direction and Speed of the Actuator
The control valve regulates the direction and speed of the actuator. In turn, it regulates the flow of hydraulic fluid to the cylinder.
Design Considerations for Hydraulic Linear Actuators
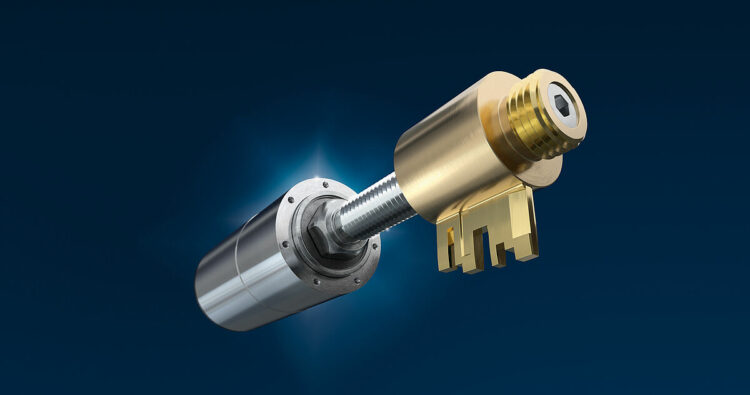
- Types of hydraulic fluids: Your selection of the appropriate hydraulic fluids should consider the operating conditions. These include temperature, pressure, and compatibility with seals and components.
- Design of cylinders: Also, choosing a cylinder type, size, and mounting style depends upon the application requirements. Other considerable factors are load capacity, stroke length, and space constraints.
- Selection of control valves: The choice of control valve often relies on the desired force, speed, and direction of the actuator. The control system requirements and compatibility with the hydraulic fluid also matter to an extent.
- Application of feedback sensors: The integration of position, velocity, and force sensors is important. They monitor and control the actuator’s movement, ensure accuracy, and improve system performance.
- Protection against overloading and environmental conditions: It is essential to apply measures such as pressure relief valves, temperature sensors, and corrosion-resistant materials. These help protect the system against overloading and harsh environmental conditions.
Applications of Hydraulic Linear Actuators
Hydraulic linear actuators are famous in a variety of industries due to their ability to provide precise and powerful linear motion. Here are some of the applications of hydraulic linear actuators.
Industrial Machinery

With heavy equipment and manufacturing machinery, hydraulic linear actuators play a crucial role. They are the best bet to ensure a smooth and efficient operation.
- Heavy equipment: Bulldozers, excavators, and loaders are among the significant hydraulic actuator applications. It enables these industrial machinery to move large amounts of earth and other materials with precision.
- Manufacturing machinery: Similarly, manufacturing machinery such as presses, stamping machines, and injection molding machines use hydraulic actuators. As a result, they generate the high forces needed to shape and mold materials.
Aerospace and Defense
Here, hydraulic linear actuators are useful due to their ability to generate high forces and operate reliably in tough conditions. Some applications include aircraft landing gear, missile guidance systems, and control surfaces.
Automotive
In the automotive industry, the main applications include steering systems, braking systems, and suspension systems. These actuators provide precise and powerful control, a critical feature for safety and enhanced performance in modern cars.
Construction Equipment
These components are also popular in cranes, backhoes, and concrete pumps. These actuators provide precise control and enormous forces for operating heavy machinery on construction grounds.
Advantages of Hydraulic Linear Actuators
Hydraulic linear actuators have several advantages that make them a popular choice in various industries. The major ones are:
- High power and force output.
- High durability and reliability.
- Wide range of speeds and force control.
- Low maintenance and operational costs.
Limitations of Hydraulic Linear Actuators
Irrespective of their many advantages, hydraulic linear actuators have some limitations. The obvious ones are:
- Potential leaks in the hydraulic system.
- Requirements for regular maintenance.
- The need for a power source to operate.
- Increased complexity.
While considering your application needs, it is crucial to carefully weigh the pros and cons of each actuator type.
Conclusion
Hydraulic linear actuators are an essential component in many industries, providing powerful and precise motion control for a wide range of applications. Their ability to produce high force and torque while also maintaining accuracy and speed makes them a popular choice for industries such as manufacturing, construction, and aerospace.
By understanding the basics of how hydraulic linear actuators work, it becomes easier to select the best type of actuator for a specific application, troubleshoot any issues that may arise, and maintain the proper functioning of the actuator for optimal performance and longevity.