Aluminum extrusion machines have become a game-changer in the manufacturing industry, especially in the production of modern car equipment. These machines play a crucial role in shaping aluminum into various components used in the automobile industry. In this section, we will delve deeper into understanding what aluminum extrusion machines are and how they came into existence.
The Rise of Aluminum in the Automotive Industry
Aluminum has been steadily rising in popularity within the automotive industry due to its unique properties and benefits. In recent years, we have seen a significant increase in the use of aluminum in modern car equipment such as body panels, structural components, and engine parts.
This trend is expected to continue, with experts predicting that aluminum will become even more prevalent in the automotive industry in the coming years.
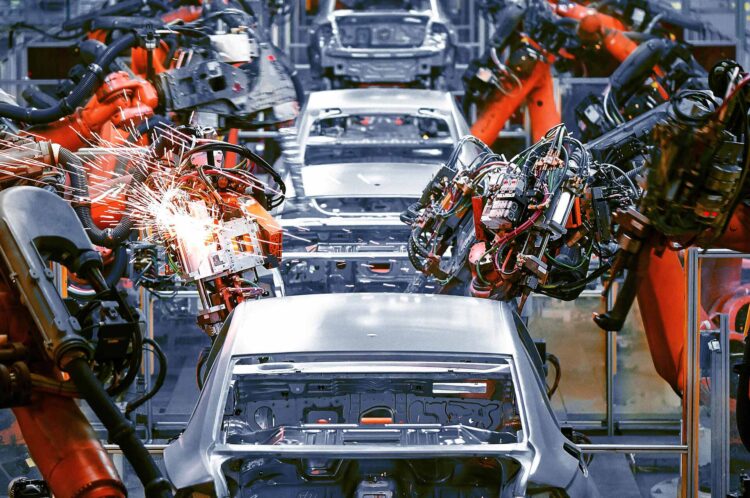
One of the main drivers behind this rise is the pursuit of lightweight materials that can improve fuel efficiency and reduce emissions. As government regulations on fuel economy become stricter, automakers are turning to aluminum as a viable solution.
It is much lighter than steel and can help reduce the overall weight of a vehicle by up to 30%, thus improving fuel efficiency without compromising on safety or performance.
Furthermore, aluminum has an excellent strength-to-weight ratio compared to other materials commonly used in cars. This means that less material is needed to achieve the same level of strength as heavier metals like steel. As a result, a vehicle made with an aluminum extrusion machine is not only lighter but also stronger and more durable.
Another advantage of aluminum is its formability. It can be easily molded into various complex shapes through processes such as extrusion – which involves pushing heated metal through a die – making it an ideal material for creating intricate structures like car frames.
With extrusion technology constantly improving and becoming more advanced, we are now seeing more sophisticated designs being utilized in modern automobiles.
Benefits of Using Aluminum Extrusion Machines in Car Equipment Production
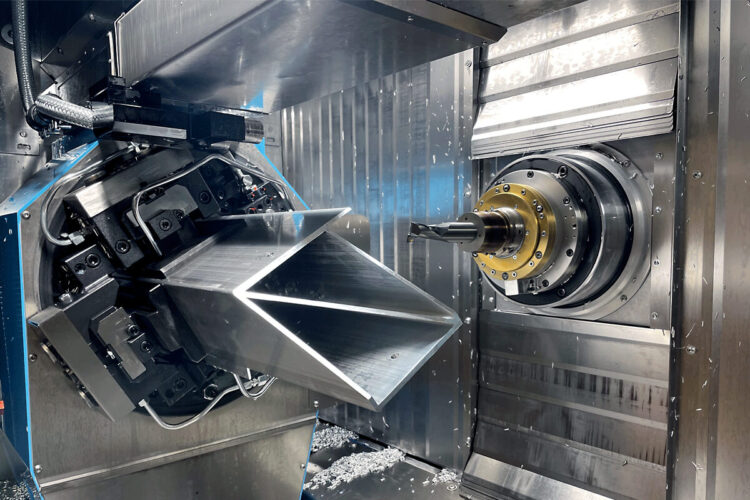
There are many benefits to using aluminum extrusion machines in the production of car equipment. From increased efficiency to cost savings, this advanced technology is revolutionizing the way modern cars are made.
- Lightweight and Strong: Aluminum extrusion produces components with a high strength-to-weight ratio, essential for fuel efficiency and performance in vehicles.
- Design Flexibility: This technology enables the creation of complex shapes and detailed designs, perfect for custom car parts.
- Durability: Aluminum parts are corrosion-resistant and withstand extreme temperatures, ensuring long-lasting performance.
- Cost-Effective: Aluminum extrusion machines streamline manufacturing, reducing labor, waste, and energy costs.
- Efficient Production: These machines enable quick production of high-quality parts, meeting tight deadlines and enhancing customer satisfaction.
Advanced Features and Capabilities
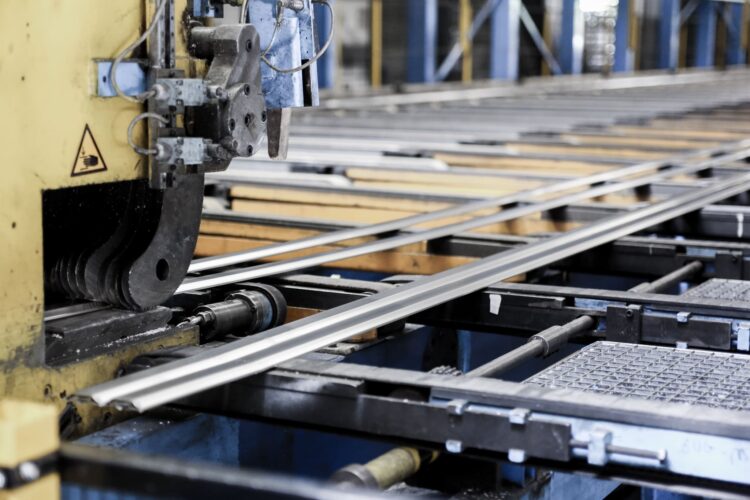
Modern aluminum extrusion machines have come a long way from their early days and now offer advanced features and capabilities that have revolutionized the manufacturing process of car equipment.
These advancements in technology have greatly improved the efficiency, accuracy, and versatility of these machines, making them an essential tool for any car equipment manufacturer.
Here are some of the most notable advanced features and capabilities of modern aluminum extrusion machines:
- CAD Integration: Modern machines integrate with computer-aided design (CAD) to transfer 3D models directly to the machine, enhancing accuracy and efficiency.
- Smart Control Systems: Equipped with sensors and actuators, these systems precisely control extrusion parameters, minimizing errors.
- Multi-Cavity Extrusions: These machines can produce multiple parts simultaneously, boosting production capacity and cost-effectiveness.
- Complex Geometries: Advanced die technologies allow for the production of intricate shapes, expanding design possibilities.
Challenges in Aluminum Extrusion Machines for Car Equipment Production
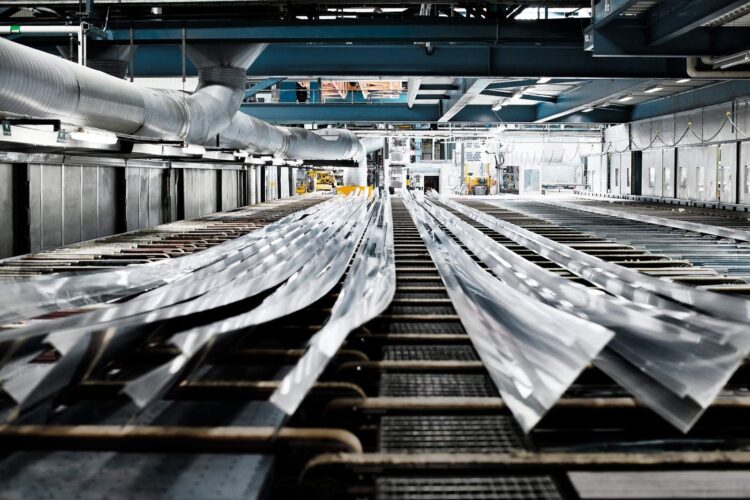
One of the main challenges faced by the aluminum extrusion industry is the growing demand for lightweight and fuel-efficient cars. This has led to an increased use of aluminum in car manufacturing, resulting in a higher demand for high-quality and precise aluminum extrusion machines.
Another challenge is the increasing complexity of car designs, which require specialized and customizable extruded components. This requires manufacturers to constantly innovate and upgrade their machines to meet these demands.
Furthermore, as the automotive industry shifts towards electric vehicles, there is a need for more efficient and sustainable production methods. This puts pressure on extrusion machine manufacturers to develop eco-friendly solutions that reduce energy consumption and emissions.
Future Developments
The field of aluminum extrusion machines for car equipment production has seen significant advancements to address various challenges. These developments include:
- Enhanced Control Systems: Modern extrusion machines have evolved with cutting-edge technology, featuring sophisticated control systems. These systems enable greater precision and offer customization options, vital for producing complex shapes that meet the stringent tolerances required in advanced car designs.
- Integration of Automation: The incorporation of automation technology in aluminum extrusion machines marks a significant leap in operational efficiency. This automation not only streamlines productivity but also minimizes the likelihood of human error. Automated systems are now increasingly being used throughout the production process, from the initial stage of loading raw materials to the final stage of packaging the finished products.
- Development of Hybrid Extrusion Machines: In response to the growing emphasis on environmental sustainability, there has been a push towards the development of hybrid extrusion machines. These innovative machines are designed to utilize renewable energy sources, aligning with the global trend towards more eco-friendly manufacturing practices. This shift not only helps in reducing the carbon footprint of the production process but also aligns with the evolving market demands for sustainable manufacturing solutions.
The Future is Bright in Automotive Manufacturing
In recent years, the automotive industry’s shift towards lightweight materials for better fuel efficiency and lower emissions has brightened the future of aluminum extrusion machines in vehicle manufacturing. These machines have evolved to be more efficient, precise, and cost-effective, allowing the production of complex, lightweight yet strong car parts.
A key advantage of aluminum extrusion in automotive manufacturing is the significant weight reduction it offers compared to steel, enhancing fuel efficiency and helping meet strict emission regulations. Additionally, aluminum’s corrosion resistance and lower maintenance needs make it ideal for vehicle parts.
This technology also provides greater design flexibility, enabling intricate shapes without sacrificing strength or durability, and encouraging innovative designs. Furthermore, with the rise of electric vehicles, the demand for lightweight materials like aluminum, which contribute to longer driving ranges, is set to increase, emphasizing the growing importance of aluminum extrusion in modern automotive manufacturing.